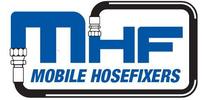
One way inline flow meter 10-100 Lpm , 3700Psi, 250 Bar
The only way to test a pump and motors safely and effectively is to use a flow meter.
OPTIONAL: This listing gives you the option to buy just the flow meter, or we can also supply a needle valve, test tee & gauge.
Typical usage;
A flow meter & pressure gauge are crucial components to check the health of your hydraulic pump or motors. When an hydraulic powered machine presents with issues of power loss or speed loss, using a flow meter is the only way to establish where the problem lays.
Hydraulic pumps & motors are very susceptible to contaminants & dirt causing wear in unmaintained circuits. If a hydraulic pump or motor is exposed to dirt etc. in the oil, or even cavitation, (air in system) the tolerances blow out very rapidly. This loss of tolerances means that normal high pressures are no longer achievable as oil simply slips past surfaces from wear.
Often hydraulic machines, ie excavators, skid steers present with loss of power to either wheel motors or lifting power to cylinders is poor. First step to check issue should be a flow test. It is good to find hydraulic specs online to find what LPM the machines pump should be producing.
Steps
Always wear safety glasses, gloves etc. High pressure oil injection can result in amputation & nasty injuries!
Have a pen & clip board to notorise numbers at certain pressure readings. ie make a sheet with zero , 500, 1000, 1500, 2000, 2500psi etc columns ready
To test a hydraulic pump first step is to attach the flow meter to the pumps pressure line. There must also be an exit hose either back to tank, or however suits to return oil from the other end of the flow meter. The oil flow from pump must go in direction of flow meters arrow (load sense pumps are excluded). On our reverse flow kits, you can use either connection, it won't matter.
Ensure the needle valve is fully open(clockwise) before starting your hydraulic pump. Set machine to correct RPM range for normal usage, remember fixed displacement pumps flow more/less depending on engine RPM. You can then write down the first reading in LPM from the flow meter on the sheet of paper. ie. 70LPM @ zero Psi. Then to mimic putting a heavy load on the pump, which is when oil would want to start 'slipping/bypassing, start turning the needle valve CW until you see pressure gauge rising. Stop at say, 500psi & again note down the LPM flow @ 500psi. Then adjust again in aprox 500Psi increments noting Lpm flow readings. Gear pumps have a normal 20% bypass rate from new, piston pumps have less. You will notice your Lpm flow rate number decreasing as pressure increases. If more than 20% below zero pressure flow rate, the pump has wear. In this case, where the pump had 70Lpm @ zero, it should still flow 52 Lpm at higher pressures if in good condition.
To test hydraulic motors, set up is similar. However a case drain hose back to tank MUST be fitted. Again you will need to find manufacturers specs on expected leakage rates.
NOTE; FLow must go in along with gauge on left-hand connection as per photos. There is an arrow on the Flowmeter.
RL 7.9.23
JH - $