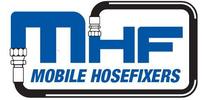
AUSTRIAN MADE OIL COOLER DC 12V / 24V These high quality Austrian made oil cooler are a high-performance product. Able to cool flows up to 300lpm. This is available in different cooling sizes, the smallest unit is a one fan unit. The rest utilise two fans for optimum cooling. To size up the correct cooler, it is imperative you supply us your machines oil flow specs. Failure to size correctly will lead to poor performance, & a cooler that is not sized correctly! A little time invested in sizing will reward with correct results. These are serious oil coolers, & weigh 30-50 Kg. The chart below indicates actual cooling performance for each size.
What figures to supply us; Oil tank size Litres per minute of system Max pressure system is run at Starting oil temp For Design assistance and sizing Please contact us by email at sales@mhfgc.com.au or phone us on +61 (07) 5563 1982 Please note, you will require extra options for these coolers 'Connector kits' these are available in four thread choices; 1.1/4",1.1/2" Bspp, 1.5/8", 1.7/8" UNO "Temp Switch" this will only start the fan when oil temp reaches 50°c,60°, or 90°c, saves wear on the fan, & stops oil being too thick on cold days. Only one of these is required for twin fan coolers, however, you must use a relay due to high amp draw of DC fan. "Temp Sensor with controller", this is an excellent long term item, that slowly raises the fan speed according to oil heat. It saves wear on the DC fan motors. Two of these are required for twin fan coolers. FREIGHT; These units are shipped ex Melb, or Ex Brisbane. Flat rate shipping will not apply to remote areas, WA etc. We will call & work out best shipping rate for remote areas. What happens when oil is too hot 1. Shorter Oil Life Hydraulic Oils or Transmission Oils operating at temperatures above 65°C (150°F) will start to deteriorate at an accelerated rate, this will result in shorter oil change periods. For Example having to change your Hydraulic System's oil every 1000 hours instead of 1500 hours or your transmission oil every 15,000 KM instead of 30,000 KM. Result more money spent on Oil and filters. 2 Gasket and Seal Damage Hot Oil damages Gaskets and Seals and this may result in Internal as well as External Leaks. 3. Internal Leaks Internal leaks reduce efficiencies, power and or torque of hydraulic cylinders, pumps and motors and in the case of a transmissions may cause erratic performance, slow acceleration and or gear shifting. 4. External leaks External Leaks can make a mess of your mobile equipment as leaks are blown all over the underside of your vehicle, dust and grime will then stick to the oily components creating an ugly sticky mess requiring cleaning. 5. Dangerous Slip Hazards Oil leaking or dripping onto a non absorbent floor or road not only makes a mess but also creates a potentially dangerous slip hazard that may result in an automotive accident with personal and property damage and possible prosecution. 6. Fines for Environment damage and Pollution Oil Leaks onto the ground could be interpreted as contamination and pollution and you risk being fined. The actual or perceived risk of environmental impact from an oil leak is real, so stop that leak or at the least clean it up and save yourself the potential of legal action and a fine or imprisonment! A recent Client of ours was sent a clean up bill for AU$3,500 when their excavator was left unattended and unchecked over the weekend leaking hydraulic oil into the ground on a particularly sensitive government construction site. 7. Mechanical Damage Large external leaks if left unchecked will reduce or deplete the oil level of the hydraulic oil circuit causing excess friction and even more heat generation, poor performance, and eventually catastrophic mechanical damage. 8. Poor Efficiency Lastly the Hydraulic system's efficiency is reduced because the oil viscosity changes (usually gets thinner) and more power losses are experienced resulting with even more heat being generated with reduced machine performance and or productivity. If on the hand you operate a piece of equipment at UNDER the oil's designed temperature range you risk the following problems. 9. Poor Oil Flow when oil is too cold. An oil that is designed to operate 10°C to 40°C ambient temperatures will be too thick to flow properly a -5°C, This can cause the machine's oil pump to cavitate which causes accelerated mechanical wear and contamination in the oil. 10. Insufficient Lubrication When a pump cavitates it is not actually pumping as much oil volume as it was designed to do and therefore not enough oil will reach critical mechanical components to produce drive, support loads, reduce friction and or carry heat away. The result is accelerated mechanical wear and or damage. 11. Temperature Control and Design. As with internal combustion engines that have water cooling and thermostats that control temperature to a relatively narrow range, thermostat control is also available for oil cooler systems to provide quick warm up and or cooling down but are also designed to prevent over cooling. To read more about problems you can expect to encounter, (look for more blue font below the following oil cooler calculations.) How to Calculate the Size of an Oil / Air Cooler. You will need a thermometer (infrared is best) to measure oil temperature and a time piece to measure the time. Pick a location on the machine where heat is experience and you know oil is flowing through it and measure at the same location every 15 minutes, record the temperature and the time. Summarise all recordings Start temperature The rise or final temperature And the time it took (in hours) for the temperature to rise to the final recording.
The theory
When there is power transfer, friction or a resistance to oil flow, pressure as well as heat are generated. The temperature of an oil in a circuit will continue to increase until the added thermal energy has the same value as the combined radiation and convection energy absorbed by the surrounding atmosphere. After a certain operating time the oil temperature rise will eventually slow and then stabilize. If this stabilized oil temperature is too high, the oil must be cooled because Hot Oil will Cost you in repairs, a lost job, or a lost race! In order to choose the required cooler type we must know the required cooling performance. How to find out the required Oil cooling requirement. Example A. With the rise in Oil Temperature For existing Hydraulic / Oil circuits the heat input to the oil can be accurately determined if the rise in the Oil's temperature is measured over a certain period of time. This then gives the amount of heat to be exchanged by the cooler in order to maintain the system at an optimum operating temperature. PK = m x c x (t2 – t1) / 1000 x T PK = required cooling performance [kW] m = Weight or mass of the oil in reservoir [kg] (see below for how to calculate this) c = specific heat capacity [Wh/kg°C] (c ~ 0.53 for hydraulic oil, c ~1.16 for water) t1 = oil temperature at the begin [in °C] t2 = oil temperature at the end [in °C] T = heat up time [hours]
To Quickly Calculate the Oil weight or Mass (in Kilo Grams) of the hydraulic oil in a tank use the following formula. Length x Width x Height of tank in cm then multiply by 0.00088 pic$ RL 15.12.20 RR$ 20-12-2021 |
IMPROPER SELECTION, INSTALLATION, IMPLEMENTATION AND/OR OPERATION BY ANYONE OTHER THAN PERSONS WITH APPROPRIATE TECHNICAL AND MECHANICAL TRAINING CAN RESULT IN DAMAGE TO EQUIPMENT OR PROPERTY, SERIOUS PERSONAL INJURY OR DEATH. PROPER PRECAUTIONS AND SAFETY PROCEDURES SHOULD BE IMPLEMENTED PRIOR TO INSTALLATION AND OPERATION OF EQUIPMENT.